As a business owner, making the most of your resources or maximizing your outputs from your given inputs is the type of business efficiency you strive to achieve. If you haven’t considered how to increase your company efficiency, you may be neglecting opportunities to reduce the amount of time you spend on a specific activity.
According to a study by Direct Air, one single 3mm hole can be costing your business £600 due to air leaks in super silent air compressors, wasting 20% to 40% of the air generated in a manufacturing plant.
How much does a leak cost?
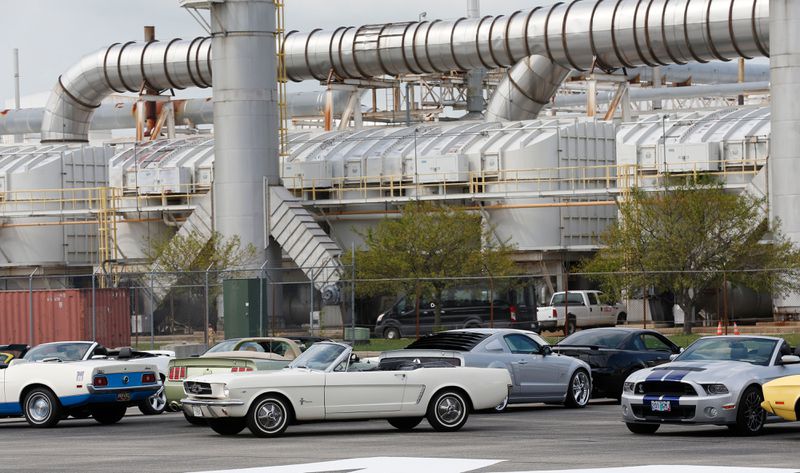
Quiet compressor air systems are useful in a wide range of applications. Compressed air is one of the most expensive and essential services in many industries, so even a minor leak may be costly.
Even though air leaks are an inevitable business expense, they may be costing firms money each year owing to unnecessary energy losses as further research by Direct Air showed that businesses lose over estimated £100 million each year due to air leakages and if such companies regularly maintained their silent air compressors they’d save £37,000 per year.
A compressor requires roughly 7 to 8 HP of electrical power to produce 1 HP of compressed air power, and this is a relatively expensive conversion rate, so any leakage is costly.
Identifying and Preventing Air Leaks
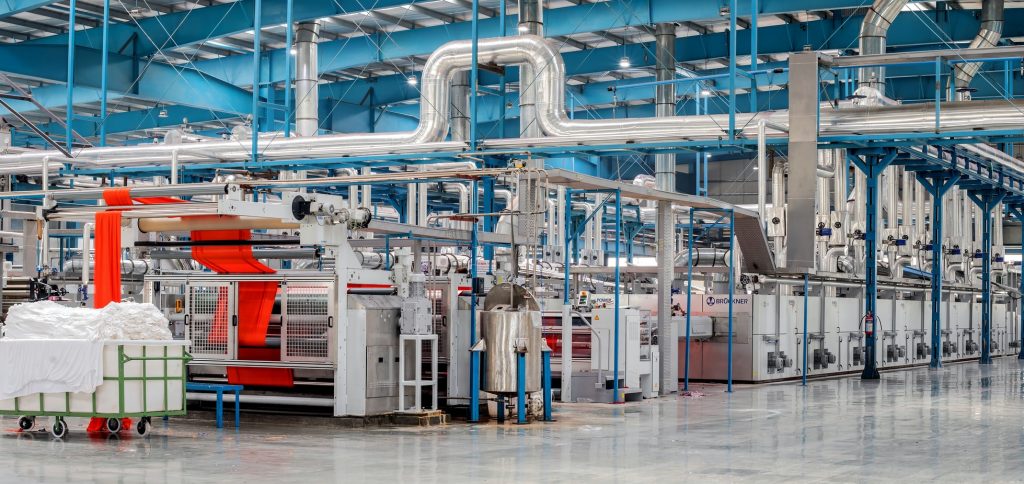
Identifying the source of the problem and fixing it is the first step in preventing losses due to compressed air leakage. Air leaks might go undiscovered for years, resulting in wasted energy expenditures until the problem is addressed.
The methods for detecting air leaks include.
Keep an ear out for any noise that could be leaking
Although you can detect air leaks using your hearing, the precision is limited. Run each piece of equipment independently, then listen for leaking noises. Unfortunately, it does not work during business hours, so you’d be wasting even more time listening for air leaks.
Finding large leaks is simpler; the issue is discovering minor breaches that go unnoticed.
Inspection of Pipes
To begin, make a lather using water and soap. Soak a sponge in the liquid and clean all of the equipment’s pipes with it. When compared to what professional air compressor services can give, this approach takes time and is wrong. If there are air leaks, the lather will produce bubbles in the region where the air is seeping.
Examine the equipment
By checking around the equipment, you can find air leaks. Making lather by combining water and soap is one method. Apply the mixture to the pipe with a sponge to see where the lather bubbles up, including the valves, flanges, and joints. The issue with this approach is that it is inefficient and inaccurate.
Ultrasonic Detector
One of the most efficient techniques for detecting air leaks is to use an ultrasonic detector. The microphone in these electrical devices is set to pick up high-frequency harmonics created by leaking high-pressure gas. The circuitry uses the heterodyne concept to alter the frequency of the detected signals so that you can hear them through headphones.
Ultrasonic leak detectors can quickly determine if access is required to discover leaks in difficult-to-reach areas. With a range of up to 8 meters, operators can promptly scan air/gas distribution systems, and models with detachable sensors make testing in tight spaces easier.
Even during business hours, you may buy or hire specialists to check for air leaks. Although in-house staff may manage the sensor, it is recommended that a professional be hired.
Some ultrasonic detectors enable the user to enter the sensing distance, line pressure, and average cost to create a compressed air volume unit. They may calculate leak cost and flow rate estimations.
The detectors employ laser pointers and graded microphone probes or sensor tips for locating even the tiniest breaches so that you can mark them for subsequent repair.
The degree of leakage is related to the area of the orifice and the line pressure. Owing to the difficulties in identifying leakage, maintenance staff should check high-pressure lines first.
Benefits of fixing air leaks
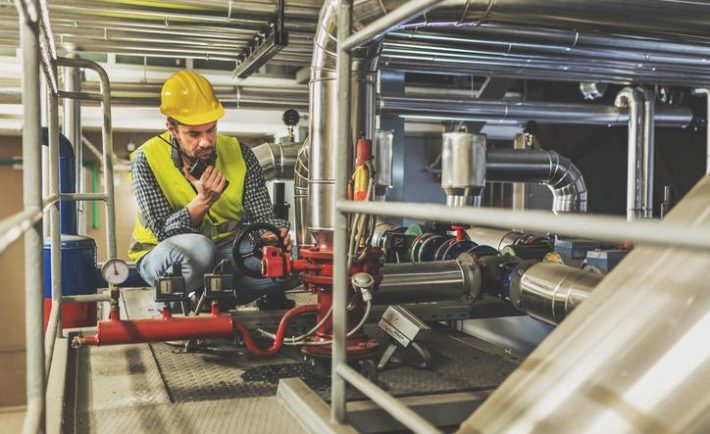
While low noise air compressors are a pleasure to operate, it is critical to ensure that lost air is not draining your cash base. Below are a few of the advantages of repairing your air leaks on time
Increased Equipment Productivity and Efficiency
Leaks may have a significant impact on your plant’s production by causing equipment to function inefficiently and creating a less productive environment. Fixing the leak will improve the equipment’s efficiency.
Increased Equipment Longevity
Due to the increased demand for air caused by leaks, low-noise compressors must cycle more frequently, reducing the lifespan of a compressed air system. This might be an expensive expense that could be avoided by undertaking routine leak detection and repair examinations.
Reduced maintenance expenditures
Air leaks not only reduce the life of your compressor by placing additional pressure on it, but they also entail more frequent repairs and maintenance expenditures than if the compressor is performing at its best all of the time.
Reduced Downtime Losses
If your system is overworked and requires repair, you will have downtime that severely impedes production and revenues.