It’s not shocking news to learn that beverage and packaging companies are constantly fighting an uphill battle against product breakage which often occurs during the shipping process. Breakage and damage can result in significant annual losses that in some cases, can greatly affect the annual bottom line.
But are there any solutions to the damage problems on the horizon? One answer to limiting the amount of breakage that occurs during transportation is to install a shock logger in every transport vehicle. According to a new report, shock loggers or what’s also known as shipping monitors, can be used for reducing the damage that occur when transporting goods which also means a reduction in monetary losses.
What it comes down to, is that utilizing shock loggers during the shipping process can not only save you money, but it optimizes the process. It’s the bottom line that counts when it comes to beverage and package shipping and finding ways to eliminate as much breakage as possible is of the utmost importance.
What Exactly is a Shock Logger?
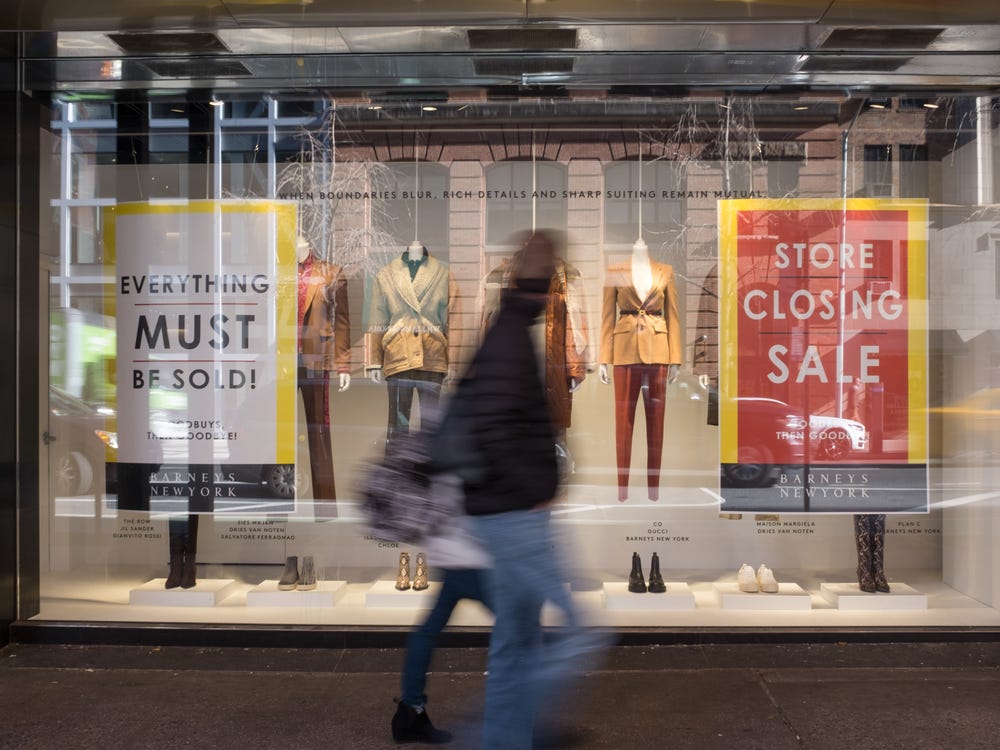
Shock loggers/shipping monitors are electronic devices that are engineered to provide “dock to dock” data and measurements of anything shipping related. While shocks (such as pressure, bumps, and rattling) plus general temperature are said to be the two most common pieces of data that’s examined on a consistent if not constant basis, shock loggers will also measure tilt, humidity, light exposure, and more. More importantly, they will also give you readings on vibrations, pressure, and impact.
Said to operate in a similar manner to the “damaging variables” that are electronically monitored via smart in-line sensors during the production process, shock loggers will measure denting damage, glass breakage, crush damage, and packaging damage during shipping.
Occasionally referred to as “transport condition monitoring,” information and data that’s gathered from pressure loggers, temperature loggers, and shock loggers, is said to be accessible in real-time. That said, the information is usually examined at the journey’s end. The data can be attached to other shipping applications by using IoT tech for analysis.
Why Shock Loggers are Essential for Shipping and Packaging Companies
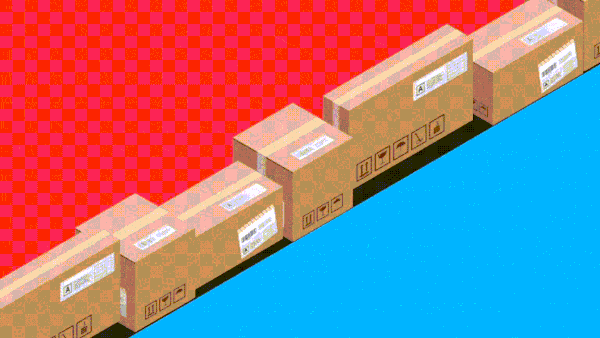
By constantly monitoring the dock to dock storage and shipping process via shock loggers, you can target where, when, and how container damage is taking place and therefore seek ways to eliminate it. The analysis of data should result in some good and productive decision making. By being aware of the root causes of shipping damage, you can take decisive action. You can also realize a real cost savings as your shipping process improves.
Say the experts, the overall benefits of utilizing “sophisticated sensor-enabled devices” like shock loggers to oversee transport condition monitoring is a crucial part of the supply chain connection.
You can now receive, via your smartphone is necessary, real-time data concerning shipping monitoring, storage monitoring, plus data measurement and analysis. You can also get real-time alerts regarding bad shipping conditions.
Companies Increase in Value When Monitoring Beverage and Packaging Transport
It should come as no surprise that one of the greatest challenges for beverage and packaging transport companies is the damage that occurs during the handling, shipping, and storage processes. In fact, billions of dollars are said to be squandered every year due to damage. That’s why the information that can be gained through electronic shipping monitoring can, in both the short and long run, allow for a “loss prevention strategy” to be implemented.
Says one shipping expert at the International Conference on Management of Technology, utilizing smart tech in both transport and warehousing such as localization, sensors, and communication tools benefits overall supply chain management.
When broken down, the increased value beverage and packaging shipping firms get from deploying monitoring tools like shock loggers are the following:
–dock to dock loss measurement
–traceability of damage causes
–the ability to quantify cost savings via real-time data
–reduction of product and glass damage during the shipping process
–proactive approach to loss prevention and food safety
–quality planning and strategizing
–the identification of root causes of product breakage
With all these benefits at hand, taken along with declining prices of shock and shipping monitors, it’s not impossible to envision a future where all shipping containers and vehicles are equipped with the smart sensors. What this will mean for the beverage and packaging industries is an increased bottom line. It will also be a boon to the connected supply chain in general.