Engines are the lifeblood of any business and take up the largest expenses. Business owners consider them as one of the most important assets to keep the business running. But what happens if that asset breaks down?
Whenever an engine breaks down, everything will get disrupted, including the performance, productivity, and overall operations. This can be difficult if your business is catching up on required outputs for the day, and the team requires an effective and quick solution.
For instance, if you own a small boat or a large ship with marine bilge pumps, it’s important to keep the engine running to prevent flooding and save your ship from sinking. Without a functioning bilge pump, a lot of things can go wrong by incurring more damage to your assets.
Deciding whether to repair or replace an engine is a tough decision for those who run a business that relies on heavy equipment. The decision lies on several factors, such as the cost, efficiency, and lifespan. To help you decide, we’re breaking down the three most critical factors when choosing whether to repair or replace an engine.
Costs
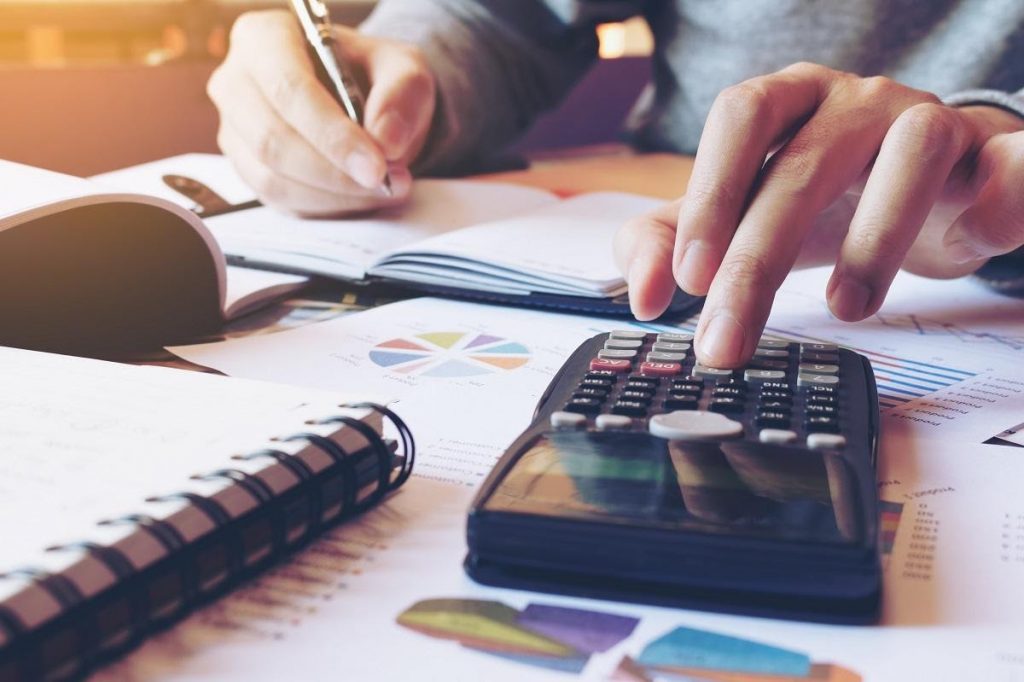
When analyzing the cost of repairs or replacements, think long-term. Determining the engine cost is fairly easy, but computing the repair cost of an existing engine is another story.
Calculating the cost of a new engine involves the service life, operational costs, potential salvage value, and revenue increase. But for old engines, you have to consider all the associate repair costs, including the labor, spare parts, losses incurred during downtime, losses during machine calibration and test period, and waste collection and removal.
From these figures, estimate the maintenance costs of getting a new engine and the old one. This involves knowing the mean time between failures (MTBF) and the amount required to reinvest for repairs. If the calculations show that going for repairs means spending more than buying a new engine, then it’s probably best to replace the equipment.
Comparing these costs can make a big difference when identifying the annual average cost of each option. In the process, you’ll learn that it’s worth cutting losses and paying more to save yourself from costly maintenance costs.
When keeping track of repair costs, document the repair events of every engine and other assets. This will give you an idea about the frequency and number of breakdowns and how much you’ll be paying for future repairs. It will also identify if a certain engine will only require a one-time fix or multiple repairs per year.
Efficiency
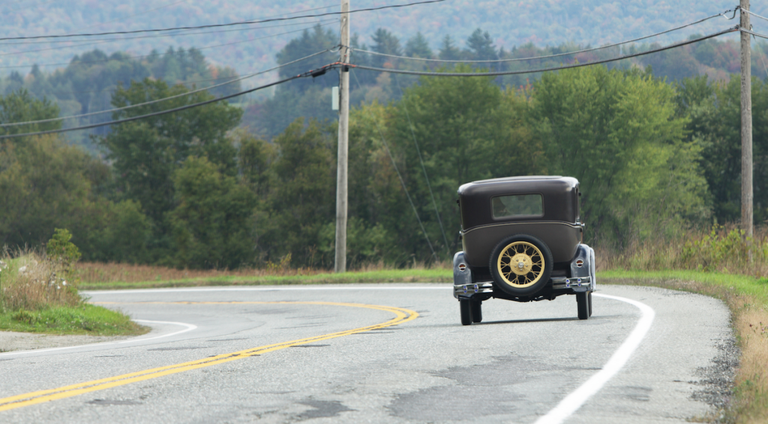
Just like costs, it’s important to think long-term when considering the efficiency of the engine. Older machines often have poor efficiency because they go through frequent downtime and have a lower performance rate than brand-new equipment.
The best way to analyze equipment efficiency is to use a computerized maintenance management system (CMMS). This type of software tool centralizes and systematizes all data related to maintenance management. It will help you decide whether you need to repair or replace a certain engine. You may find this helpful if your business relies on industrial equipment, experiences costly breakdowns, and manages large facilities and infrastructures.
When we talk about energy costs, it’s pretty obvious that older machines are notorious energy consumers. They have a low energy efficiency rating, which means they’re less efficient than new equipment in terms of energy usage.
In terms of safety, older machines have a higher risk of causing major accidents in the workplace once they malfunction. Although your equipment receives regular maintenance, you cannot stop it from wearing down as it ages. So before making a decision, inspect the machinery and determine if the equipment can contribute to maintaining a safer workplace for your workers.
Lifespan
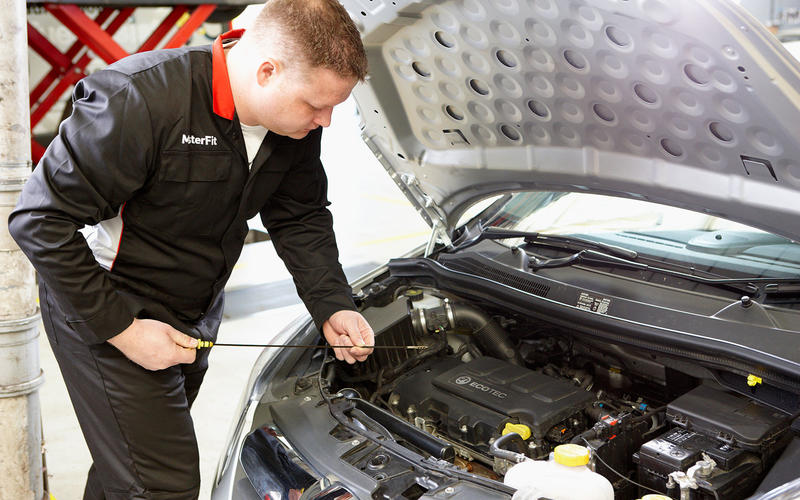
Unlike people, equipment doesn’t age with grace. Whether we like it or not, engines get worse over years of usage. So the older the equipment becomes, the more you’ll be paying for extensive repairs and higher maintenance expenses.
Every year, machine manufacturers release new models and pull out older units. As a result, it will be more difficult and impossible to get the spare parts you need, unlike the latest units.
Any equipment nearing the limits of its lifespan involves more maintenance costs, whether corrective or preventive. Thus, it’s critical to review the life expectancy of certain equipment before deciding to repair or replace it.
When deciding whether to repair or replace an engine, it’s important to make informed decisions first. Equipment tools such as engines and heavy machines perform critical work that keeps operations running and affects your business’s bottom line and overall efficiency. So the next time one of your equipment breaks down, consider the discussion above to get the best possible value out of your equipment.